Ultrasonic testing uses transmission of high frequency sound wave into a material to detect imperfections within the material or changes in material properties. The most commonly used Ultrasonic testing method in pulse echo , where sound is introduced into test object and reflections are returned to a received from internal imperfection and geometrical surface of the part.
Our ultrasonic testing services range from manual thickness reading to large scale automated corrosion and flaw detection thickness mapping using the latest ultrasonic logging systems and data acquisition software. Our skilled Ultrasonic technicians can provide manual weld examination for various application, including piping ,vessel, plate, forging ,casting,& forming.
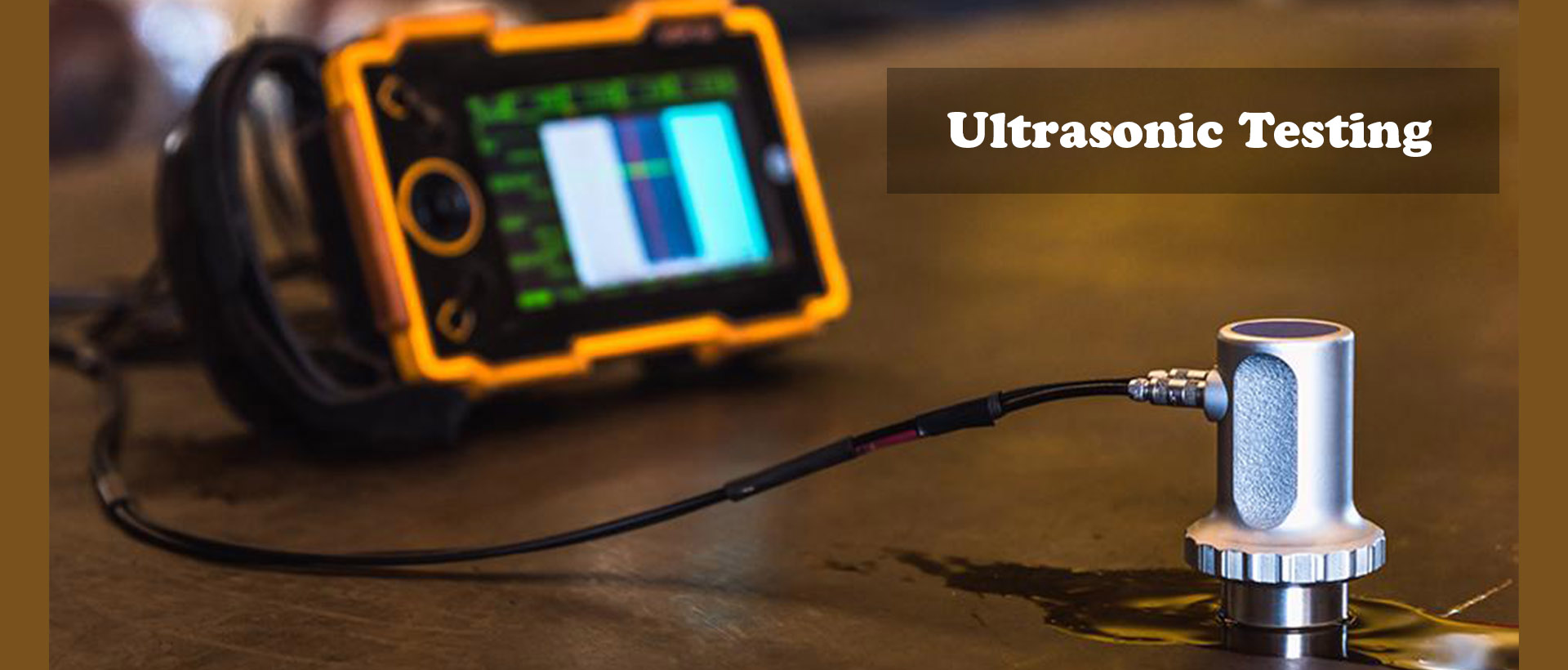
Magnetic particle inspection (MPI) is a non-destructive testing (NDT) process for detecting surface and slightly subsurface discontinuities in ferroelectric materials such as iron, nickel, cobalt, and some of their alloys. The process puts a magnetic field into the part. The piece can be magnetized by direct or indirect magnetization. Direct magnetization occurs when the electric current is passed through the test object and a magnetic field is formed in the material. Indirect magnetization occurs when no electric current is passed through the test object, but a magnetic field is applied from an outside source. The magnetic lines of force are perpendicular to the direction of the electric current which may be either alternating current (AC) or some form of direct current (DC) (rectified AC).
The presence of a surface or subsurface discontinuity in the material allows the magnetic flux to leak, since air cannot support as much magnetic field per unit volume as metals. Ferrous iron particles are then applied to the part. The particles may be dry or in a wet suspension. If an area of flux leakage is present the particles will be attracted to this area. The particles will build up at the area of leakage and form what is known as an indication. The indication can then be evaluated to determine what it is, what may have caused it, and what action should be taken, if any. UNIT NDT SERVICE gives a wide range of equipment for different kind of job & all equipment are calibrated under NABL calibrated lab.
Our Experience Include
- FAG BEARING INDIA LTD
- ALSTOM PROJECTS
- SIEMENS LTD
- L&TMHI
- THERMEX LTD
- VOITH HYDRO
- SUZLON ENERGY LTD
- ANDREZ HYDRO
- NPCIL
- BARC
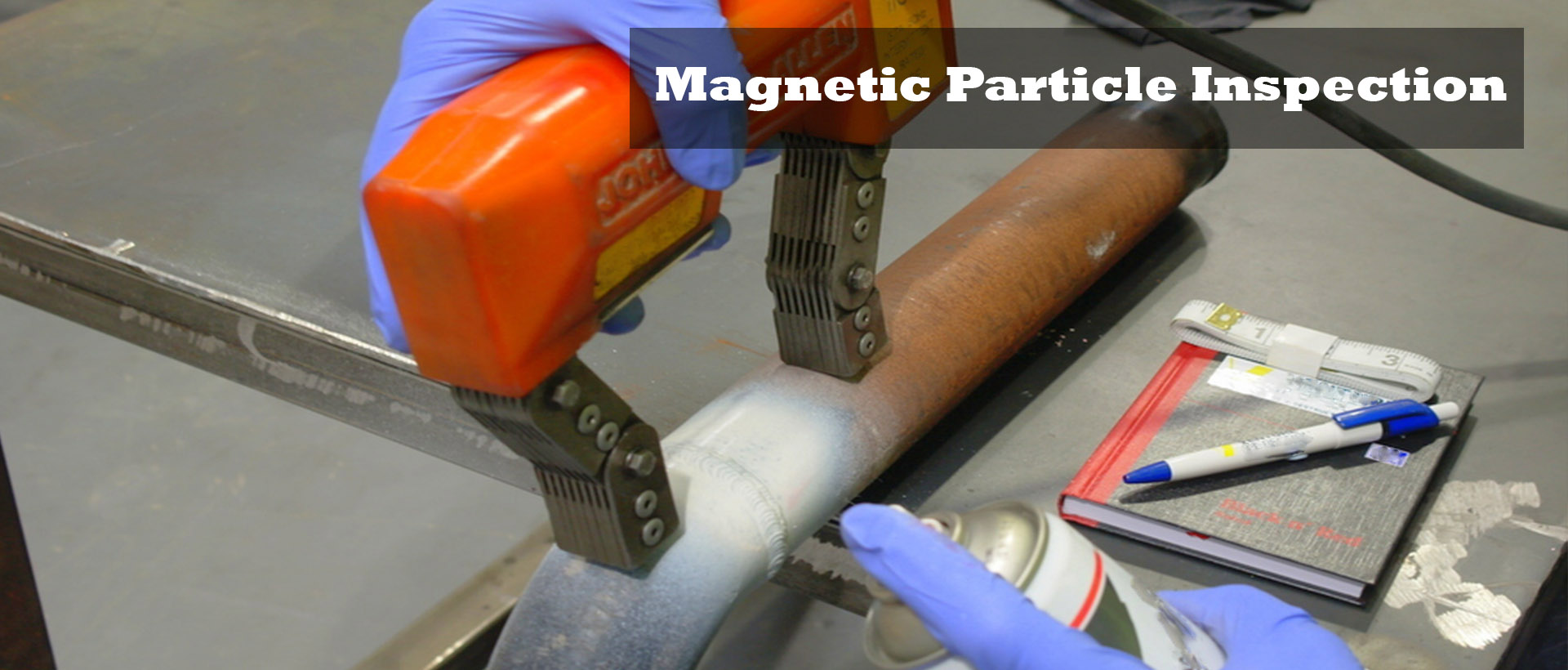
Liquid penetrant inspection (LPI), also known as dye penetrant inspection (DPI) or penetrate testing (PT), was first developed in the early 1940s to detect flaws on the surface of materials. Although there are more options in the way the test is performed, the basic principles have not changed over the years.
Liquid penetrant inspection is a nondestructive test method which does not harm the samples or parts being inspected. The test is very effective in detecting porosity, cracks, fractures, laps, seams and other flaws that are open to the surface of the test piece and may be caused by fatigue, impact, quenching, machining, grinding, forging, bursts, shrinkage or overload. As a result, it is often used on lots of machined parts, as well as weldments, manufactured products, castings, forgings and other items that will be placed into service. Liquid penetrant inspection can be used successfully on nonporous and fairly smooth materials such as metals, glass, plastics and fired ceramics.
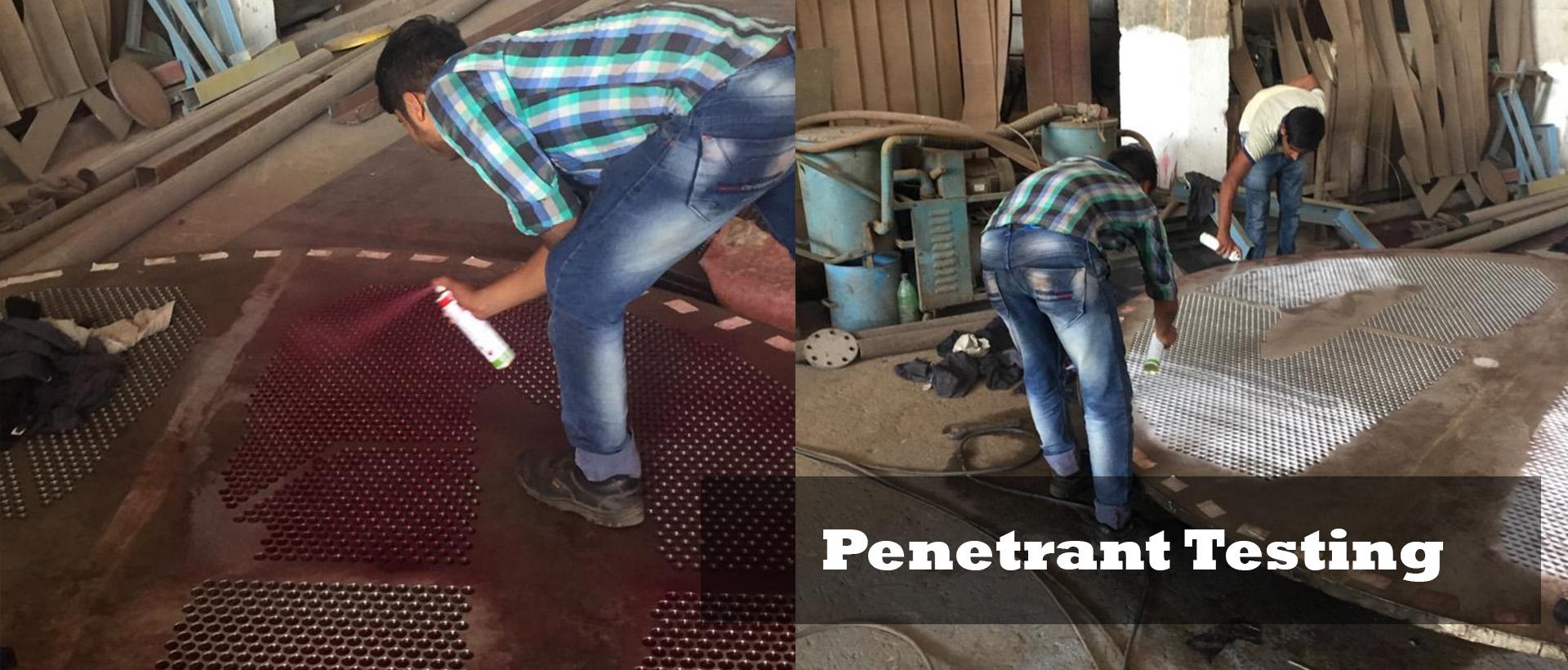
UNIT NDT SERVICE provides pipeline scanning services for piping that is above ground and un insulated. The piping can be painted or have a coating and still be scanned. we use A-Scan Ultrasonics to prove-up any flaw indications. This technology is applicable to magnetic and non-magnetic piping. Cast Iron or other cast materials can also be tested.
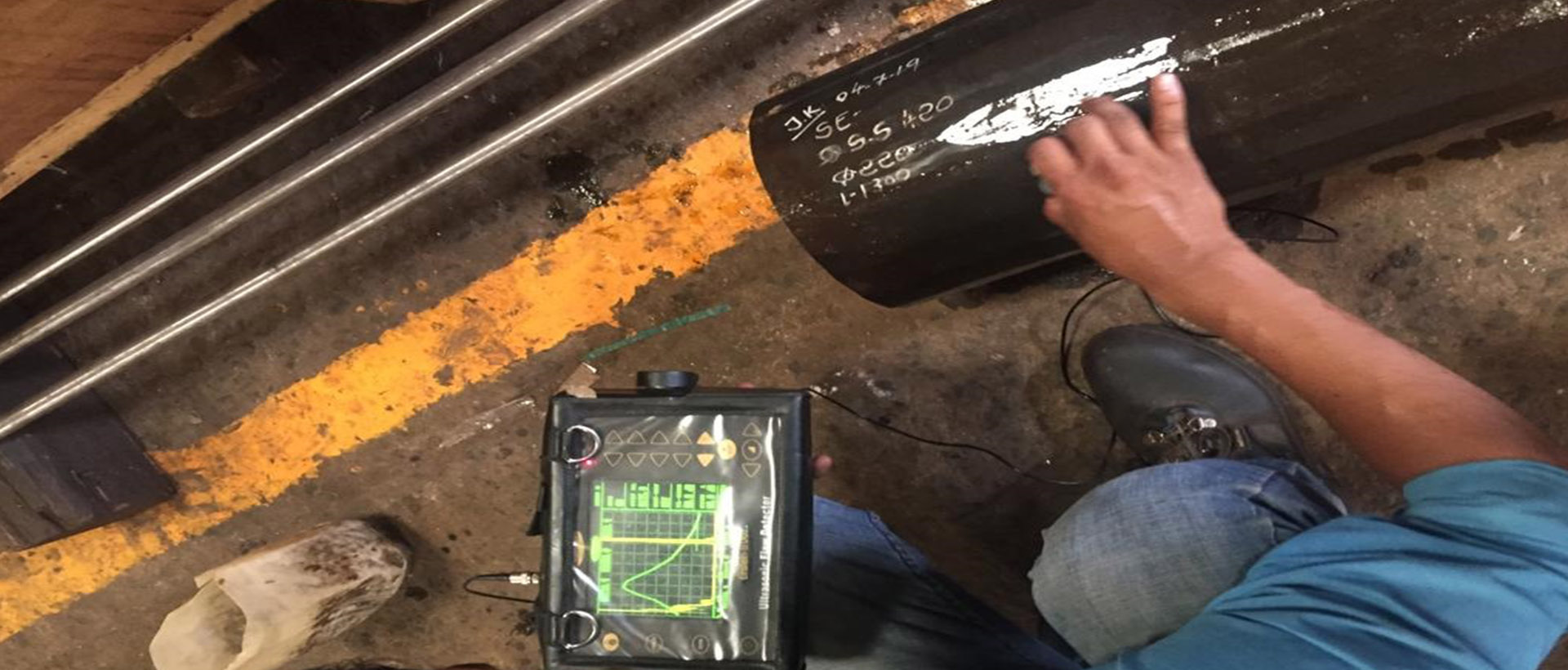
Various types of pressure vessels can be inspected using the Low Frequency Electromagnetic Technique (LFET). Using LFET, the actual wall plates can be inspected from inside or outside the pressure vessel.. Thus, a complete inspection of the pressure vessel can be performed. Our highly trained staff can also provide Dye Penetrant, Magnetic Particle, and Ultrasonic, hardness test inspection service. We have a special skilled & experienced team for NDT testing of hydrocarbon storage tank as per SMPV requirement.
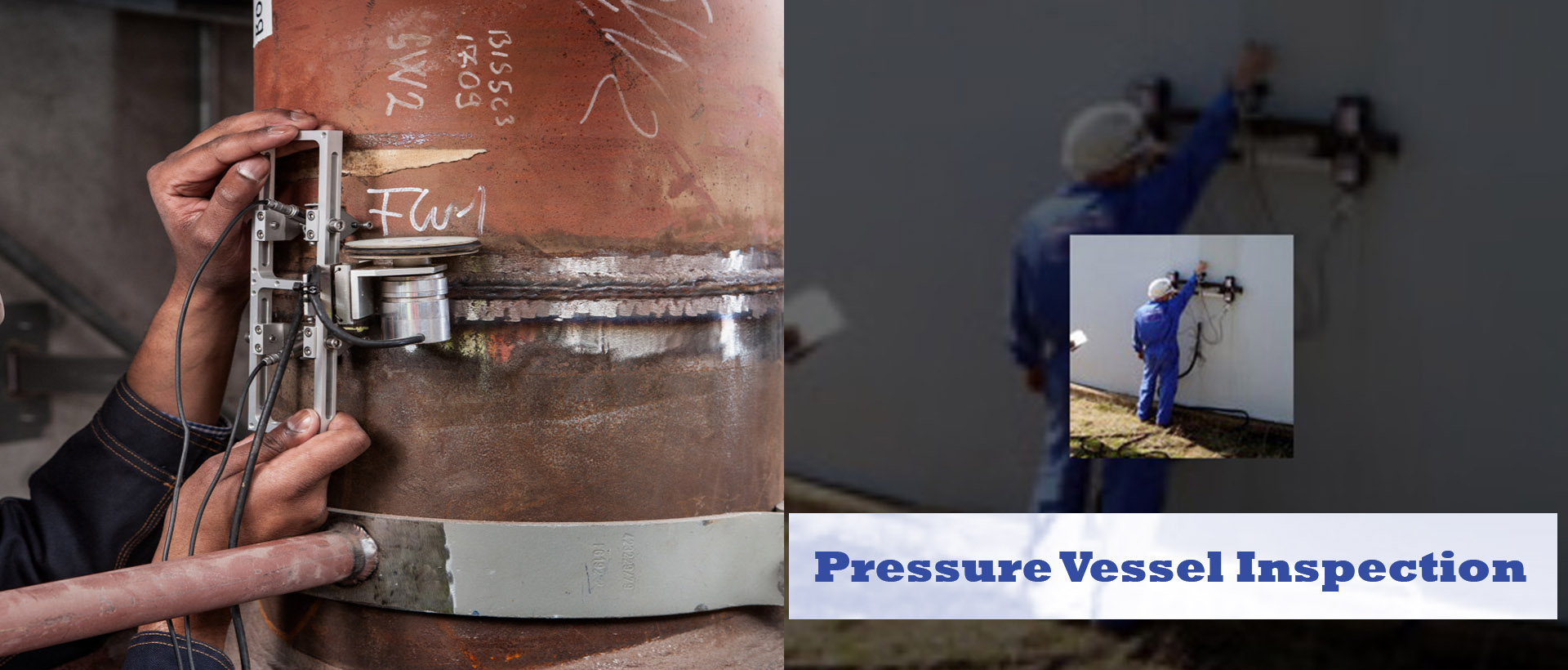
With regard to metals, hardness has always been a subject of much discussion among technical people, resulting in a wide range of definitions. Hardness properties include such varied attributes as resistance to abrasives, resistance to plastic deformation, high modulus of elasticity, high yield point, high strength, absence of elastic damping, brittleness or lack of ductility.
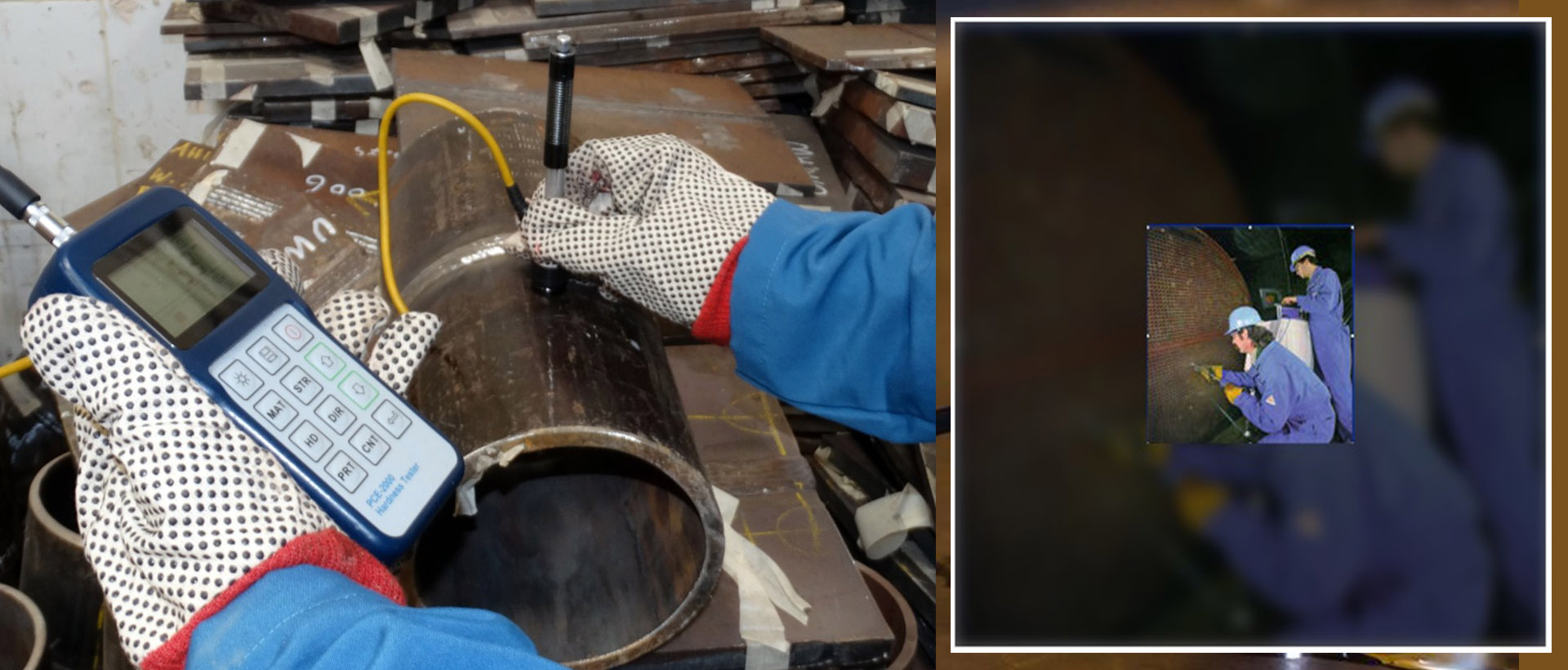
ULTRASONIC THICKNESS gauges measure the thickness of the part by measuring the time sound travels from the transducers through the material to the back end of the part, and then measures the time of reflection back to the transducer. The gauge then calculates the thickness based on the velocity of sound through the material being tested
Thickness measurement is achieved by placing the UT probe on the object surface. Local or general reductions of thickness can be located and measured with high precision. The instruments that are used for the measurement are portable and light with possibilities of saving the measurements data in a datalogger.
- we have successfully carried out thickness measurement at major refineries chemical plants
- High temperature thickness measurement
- High accuracy thickness measurement
- Corrosion mapping
Our experience include
- ONGC TANK for M/S OILEX LTD
- Inspection of pipe at GGCL/DSPC/ONGC/IOCL/RIL for TDW I LTD
- Inspection for boiler /header/drum for RAJASHREE PLYFIL, HINDALGO,GSPC,GNFC
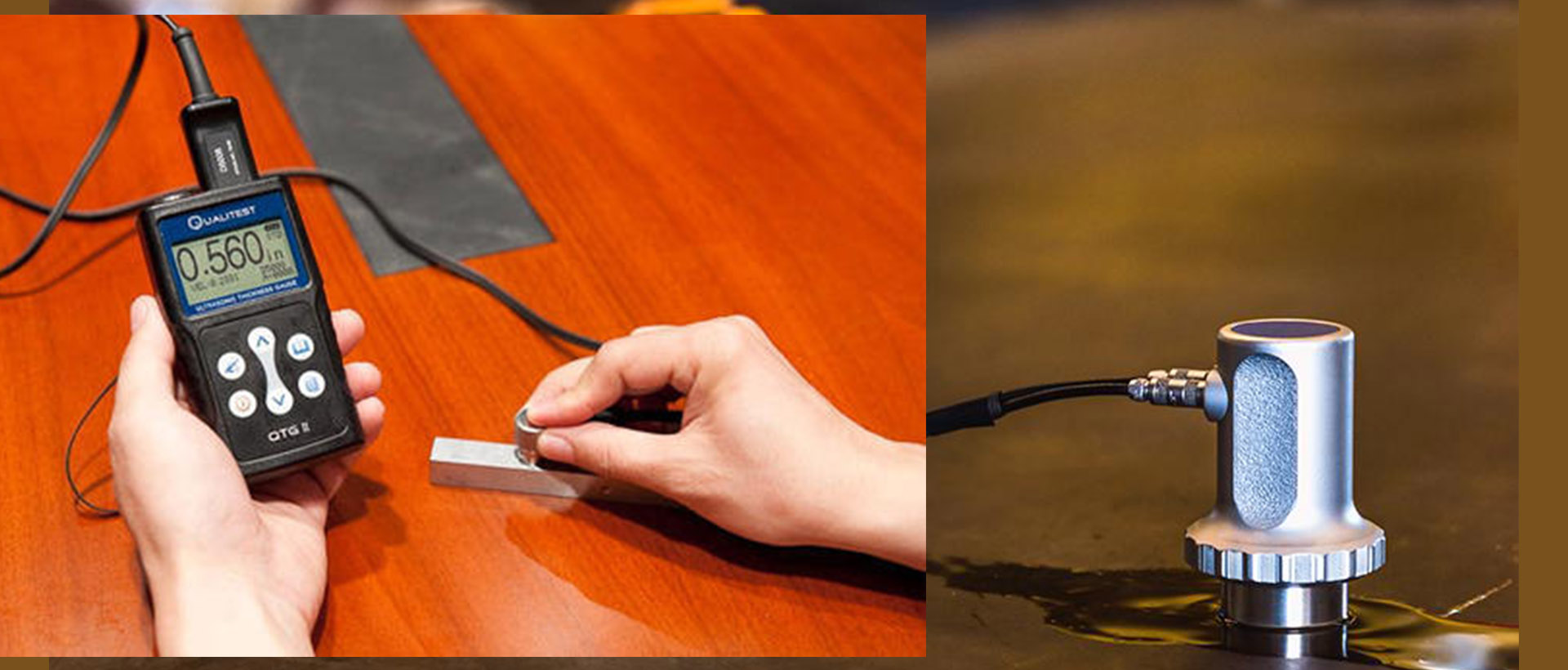
UNIT NDT SERVICE(UNS) enhances its Non Destructive Testing offering with Positive Material Identification service. UNS on-site inspection and testing team has multiple highly sophisticated handheld / portable X-Ray Florescence (XRF) Spectrometers which can measure the chemical composition of the materials, non-destructively and accurately.
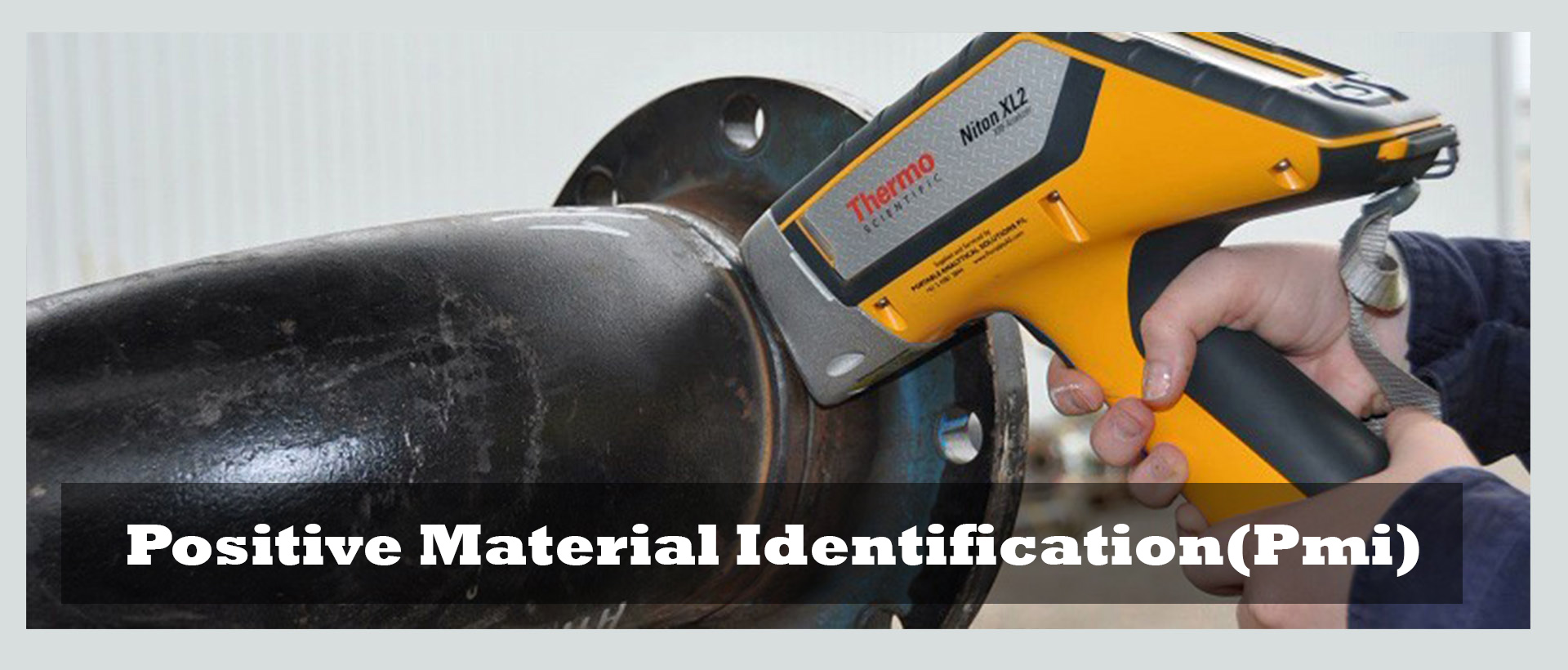
We conduct ASNT Level II Training courses at various paces all over India .We provide training in various NDT subjects like ultrasonic testing, Radiography testing ,Magnetic particle testing and Penetrant testing . We give practical hands on training on the latest equipments used in the market and also we have sample test pieces to resemble the defects which normally appear in materials. We have highly experienced Lecturers and ASNT NDT LEVEL IIIs to train the students from basics.
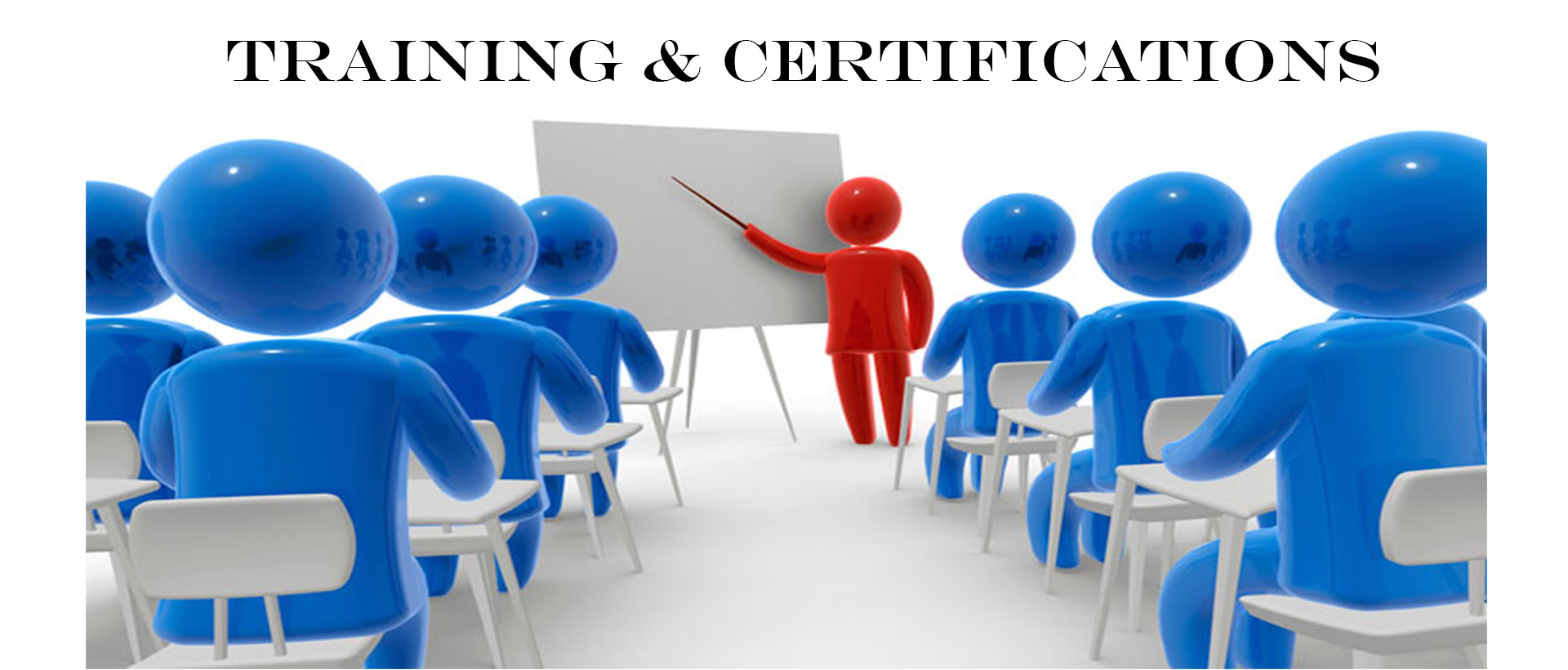